A lesson to be learned from the US-China trade war and coronavirus-induced lockdown wreaking havoc on markets and hitting mining production outlooks hard – is that North America needs to establish more robust domestic supply chains.
The US responded to the covid-19 crisis by shutting its borders and contracting production, as operations at mines worldwide ground to a halt.
Shutdowns to manufacturing plants in Beijing that could potentially cut off US rare earths exports woke the nation up to the fact that it is reliant on China for all rare earths needs.
The US government has stepped up efforts to ensure the supply of critical minerals from outside China. As part of those initiatives, it recently signed a memorandum of understanding with Greenland to conduct a hyper-spectral survey to map the country’s geology.
The $14 billion-a-year rare earth magnet market is more than 60% controlled by China which, under Made in China 2025, is increasingly using rare earth magnets in finished and semi-finished products, as opposed to exporting the magnets
Demand for rare earth magnets is being
driven mainly by electric vehicles, wind generators, medical devices, smart
phones, and aerospace and defense applications.
The $14 billion-a-year rare earth magnet market is more than 60% controlled by China which, under Made in China 2025, is increasingly using rare earth magnets in finished and semi-finished products, as opposed to exporting the magnets, says USA Rare Earth, the funding and development partner of the Round Top heavy rare earth and critical minerals project in West Texas, and industry sources estimate the rare earth magnet market will nearly double by 2027.
USA Rare Earth is also purchasing the equipment necessary to build the only rare earth magnet production facility in the Americas.
The only active rare earths mine in the US is Mountain Pass in California. After a mothball period, it is back in production – but is now owned by MP Materials, which almost a tenth-owned by a Chinese investor.
When the US Geological survey does its annual report on mills and production – the US is technically producing zero rare earths oxides because what is coming out of Mountain Pass is being shipped to China, Dan McGroarty, head of government affairs for USA Rare Earth told MINING.COM.
McGroarty said while around 2015, the Obama administration designated two rare earths, tirbium and desposium an are on the rare earths list for acquisition into the defense stockpile.
“That was at a point where there was no tirbium and desposium production in the US. Those are the two largest, by volume, rare earths that we have at Round Top. In that respect, there’s a very strong alignment,” McGroarty said.
Round Top is a heavy rare earth – dominant deposit, which is unique outside of China. It also includes uranium, beryllium, gallium, hafnium and zirconium – all of which are on the US Government’s Critical Minerals List.
“The decision that the president made last summer, under the Defence Production Act (DPA) …to designate a whole supply chain for rare earths as an urgency material under the DPA, that’s what allows the funding in the rare earths space – and there is more coming,” he said.
“We’ve got a very unique deposit in a number of respects – we have 16 of the 17 rare earths, with many in the rare earths categories that speak to a number of defense applications, and manufacturing. It is probably the largest heavy rare earths deposit in the world outside of China,” Pini Althaus, CEO of USA Rare Earth said.
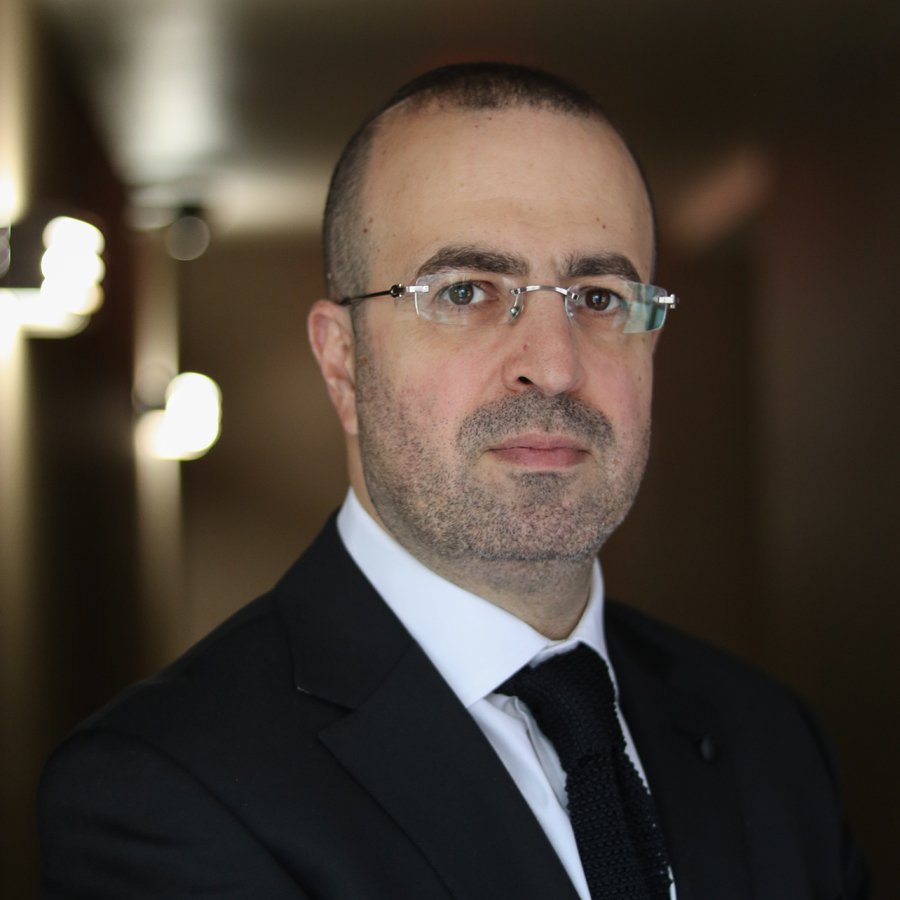
“We also have a significant amount of lithium
sulphides, so we have a very diversified project… with infrastructure in place.”
USA Rare Earth envisions a 130 year plus mine life on the project, but the PEA is focused on the first 20 years.
Althaus said they are able to heap leach the
deposit, which is rare for most rare earths deposits.
“Between our capex and opex being low – we are able to compete with China on pricing,” Althaus said.
USA Rare Earth announced in December 2019 they
are opening a pilot plant facility in Wheat Ridge,
Colorado for the purpose of fully separating and purifying rare
earth and other tech metals and critical minerals, leached from ore from
the Round Top project.
The Colorado pilot plant will be the first processing facility outside of China with the ability to separate the full range of rare earths – lights, mids and heavies.
Althaus said the plant will be moved to Texas,
where they will begin mine construction.
The Wheat Ridge plant is the second piece of a 100% US-based rare earths oxide supply chain, drawing on feedstock from Round Top.
Construction on the Colorado facility is complete, and is slated to open in the next week, Althaus said.
Early in April, the company announced that that it has purchased the neodymium iron boron (NdFeB) permanent magnet manufacturing equipment formerly owned and operated in North Carolina by Hitachi Metals America.
Round Top has been part of a Department of Defense grant, as the DOD picks the rare earths it wants processed and purified
USA Rare Earth will warehouse the equipment pending a decision about where to locate the new magnet operation, with the priority being good access to the Round Top project.
The US Military is among possible investors – and
Round Top is part of the solicitations.
There have been two solicitations that have come out of the Department of Defense (DOD). The first closed late 2019 around processing and is waiting on a response. On March 2, there was another solicitation around light rare earths.
Round Top has been part of a DOD grant, as the
DOD picks the rare earths it wants processed and purified.
USA Rare Earth announced in March the appointment of retired Army General Paul J. Kern to its board of directors.
General Kern is a member of the Defense Science
Board, established by federal law in 1956 to provide independent advice and
recommendations on scientific, technical, manufacturing, acquisitions process
and policies, and other matters of interest to the Department of Defense.
USA Rare Earth aims to have Round Top in production within 30 months, but McGroarty said if they can expedite the timeline – they will.
“The decision that the president made last
summer, under the Defence Production Act (DPA) …to designate a whole supply
chain for rare earths as an urgency material under the DPA, that’s what allows
the funding in the rare earths space – and there is more coming.”
“There will be a significant impact on the
economy,” he added. We’re talking about a $500 billion to $1 trillion impact,
in [terms of] job creation and manufacturing…everything to the electric vehicle
sector,” said Althaus.
“From a practical standpoint, one of the reasons a lot of companies have gone offshore, labour costs aside, the raw materials and processing capabilities are in China,” Althaus said. “It’s a national security issue, its an economic issue, a manufacturing issue, its job creation, and the US … is trying to bring that back home,” said Althaus.